- Home -
- Lokowanie produktu -
- Zortrax - przyszłość druku z Olsztyna?
Druk zrewolucjonizował naukę i zapewnił dostęp do wiedzy, którą wcześniej dzierżyli w swoich rękach bogaci ludzie. Drukowana biblia, potem księgi różnego typu zaczęły trafiać do mniej zamożnych, by w czasach współczesnych każdy mógł sobie pozwolić na ich niemal dowolną ilość, a obecnie można ich mieć pół biblioteki w małym urządzeniu – cyfrowa rewolucja.
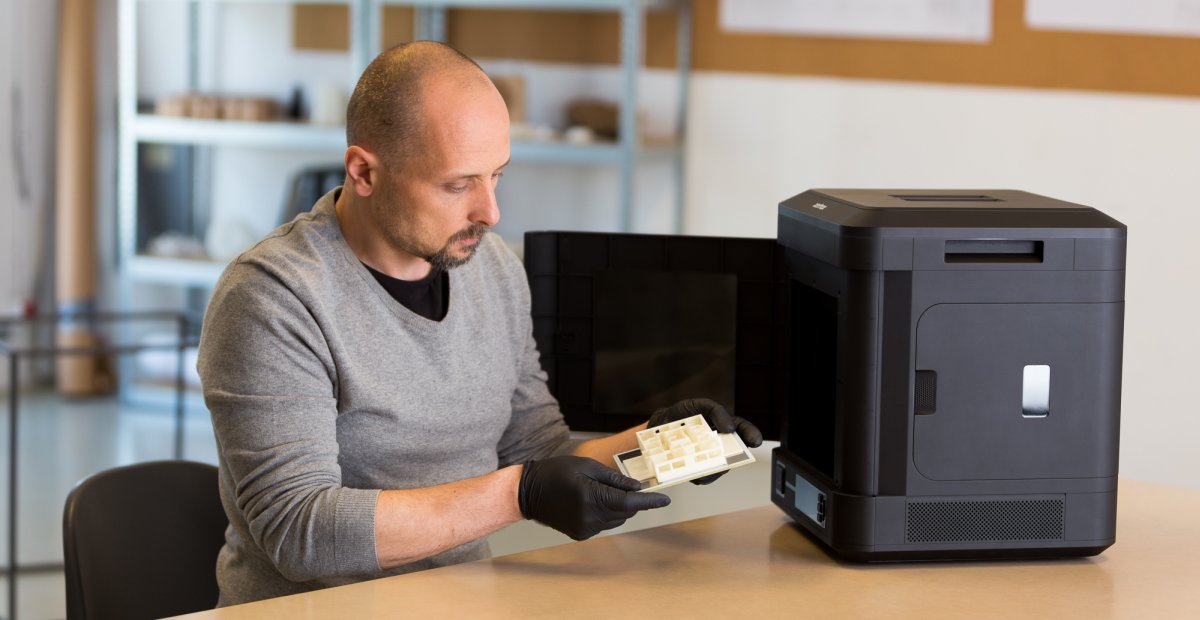
Druk. Pierwsze drewniane czcionki, potem metalowe odlewy, druk offsetowy, aż do elektronicznego papieru. Czy można było wymyślić coś lepszego? Można! Druk 3D. Szał na tę technologię rozpoczął się w momencie, gdy technika pozwoliła na budowanie urządzeń zdolnych do utwardzania materiałów w postaci płynnej lub proszkowej za pomocą laserów, światła UV i im podobnych.
Koncepcje druku obiektów trójwymiarowych snuli już naukowcy na początku lat 70tych. Jednym z pierwszych był między innymi Francuz Pierre A. L. Ciraud, który w 1973 roku opisał metodę produkcji obiektów przestrzennych z wykorzystaniem materiału budulcowego z proszku i dostarczanej energii, która miała ten proszek utrwalać.
Ciekawostką jest reż to, że ponad 50 patentów, między innymi związanych z drukiem 3D dzierży w swoich rękach niejaki Bill Masters z USA. Jednym z nich jest technologia nakładania warstw specjalnych kulek materiału plastycznego, dzięki czemu tworzone są obiekty przestrzenne.
Podwaliny pod współczesną produkcję maszyn drukujących w 3D zawdzięczamy Carlowi Dekardowi, który wymyślił koncepcję, w której do utrwalania materiału w trójwymiarze można by zastosować laser. Przypominam o metodzie opisywanej w latach 70-tych przez wspomnianego wcześniej Francuza: proszek+energia=obiekty przestrzenne.
Dekard postanowił także do zautomatyzować cały proces, który dane pobierałby z materiałów przygotowanych w programach typu CAD, czyli w środowisku projektowym zapewniającym bardzo dokładny opis graficzny obiektów w wielu rzutach – w trójwymiarze.
Współczesne maszyny drukujące 3D zawdzięczają jednak bardzo wiele innemu Amerykaninowi, a mianowicie Charlesowi Hullowi. Na proces druku 3D Charles Hull wpadł, pracując nad żywicami utwardzanymi bardzo szybko światłem ultrafioletowym. Opracował on metodę druku SLS, czyli stereolitografię. Jako jeden z pierwszych postanowił on swój pomysł przekuć w pieniądze, czyli zainwestował i założył pierwszą firmę, która rozpoczęła produkcję urządzeń do druku trójwymiarowego – 3D Systems.
Poniżej filmy prezentujące zasadę działania stereolitografii.
Pomysł i urządzenia nie zawojowały na początku rynku. Dopiero gdy znane media podchwyciły nazwę „Druk 3D” i opisywały proces tworzenia obiektów przestrzennych za pomocą urządzeń, które w pewnym sensie przypominały zasadą działania zwykłe i powszechne już drukarki laserowe lub atramentowe, ludziom zaświeciła się w głowach lampka. Zaczęły kiełkować pomysły na wykorzystanie tej technologii.
Zmieniały się metody, materiały. Stosowano wspomniane wcześniej żywice, proszek gipsowy spajany specjalnym klejem, dodawano nawet kolory do materiałów, a wszystko to działo się jeszcze w latach 90-tych ubiegłego wieku!
Dzięki drukarkom trójwymiarowym możliwe stało się w miarę szybko i stosunkowo tanio modeli trójwymiarowych różnego typu, mimo iż urządzenia kosztowały dziesiątki i setki tysięcy dolarów. Na ekranach komputerów można było oglądać renderowane modele, przybliżać je, obracać i zaglądać im we wszelkie otwory, załamania, etc., ale nijak nie dało się ich sprawdzić w realnym świecie. Do tego trzeba było zaprzęgać różnego typu obrabiarki, które w pewnych przypadkach nie są w stanie stworzyć modeli, które mają bardzo skomplikowane kształty, wewnętrzne kanały, otwory, etc. Jeśli jest to możliwe, to koszty są bardzo wysokie.
Druk 3D sprawił, że można było je szybko i bez większych problemów tworzyć. Niestety pierwsze urządzenia nie zapewniały bardzo wysokiej precyzji i dokładności, ale i tak była ona na tyle duża, że sporo firm pokusiło się o ich zakup i wykorzystywanie w procesach projektowania i tworzenia różnego typu urządzeń.
3D Systems szybko zyskał konkurencję w postaci tuzów branży chemicznej – firm DuPont oraz Loctite (Henkel). Co więcej, firmy walczyły także o patenty i to, kto komu podbierał lub wcześniej od konkurenta opracował dane rozwiązanie. Swój udział w rynku urządzeń do druku 3D miała także japońska firma SONY.
Kolejne lata przynosiły nowe rozwiązania, które głównie dotyczyły materiałów, z których tworzone były obiekty i ich utrwalania. Pojawiły się materiały termoplastyczne, takie jak polimery utwardzane światłem, specjalne folie, proszki metaliczne, woski i inne. Większość drukarek, które wykorzystywano, tworzyła modele o niezbyt dużych gabarytach, choć pojawiały się konstrukcje zdolne do tworzenia obiektów o niemal dwumetrowej długości.
Kolejnym krokiem było stworzenie urządzenia, które było zdolne do utrwalania nie pojedynczych elementów, ale całych warstw za pomocą światła sterowanego tak, jak w projektorach DLP – za pomocą ogromnej liczby mikrolusterek sterowanych cyfrowo.
Ciekawostką były prace Adriana Bowyera, brytyjskiego profesora, który postanowił stworzyć koncepcję drukarki samopowielającej się, czyli umiejącej produkować elementy mogące posłużyć do budowy identycznego urządzenia. Powstało urządzenie zwane RepRap (Replicating Rapid Prototyper).
Projekt ten zapoczątkował lawinowe powstawanie amatorskich konstrukcji zdolnych do druku 3D. Jedną z ciekawszych, jest mocno uproszczony model RepRap Mandel, którego zaprojektował Czech Josef Průš.
Jeśli chodzi o wkład Polaków w druk 3D, to mamy się czym pochwalić, choć rodzime konstrukcje pojawiają się dopiero od kilku lat. Jedną z bardziej znanych jest firma ZMorph, która zaprojektowała w 2012 roku swoje urządzenie, bazując na koncepcji open source RepRap. Przystosowali oni swoją drukarkę 3D do technologii FFF (Fused Filament Fabrication), w której kolejne warstwy powstają z rozgrzanego materiału plastycznego, który ochładzając się, staje się twardy.
Obecnie dostępne są modyfikacje urządzeń, które są w stanie drukować jedzenie, elementy ubrania, butów, a nawet całe… domy! Mechanizmy wykorzystuje się na różne sposoby, a ograniczeniem jest jak zwykle tylko… wyobraźnia i dostępne obecnie technologie tworzenia materiałów służących do druku.
W Polsce funkcjonuje firma, której historia może spodobać się wielbicielom opowieści o karierze „od zera do milionera”. Kilku pasjonatów z Olsztyna swój pomysł na drukarkę 3D przekuło w projekt, a zaczęli jeszcze w 2011 roku. Gdy wszystko było już przemyślane, opracowane i zaprojektowane, barierą pozostały finanse. Żaden z nich osobno ani wszyscy razem nie dysponowali finansami, dzięki którym mogliby rozpocząć działalność. Zaprezentowali swoje projekty jako Zortrax na portalu internetowym Kickstarter i wystąpili o fundusze na rozwój i produkcję swojego pomysłu.
Jest to serwis, w którym każdy może opisać swój pomysł, przedstawić prototyp urządzenia i poprosić o pomoc w sfinansowaniu rozwoju, produkcji, ziszczenia marzeń społeczność internetową. Ludzie głosują swoimi portfelami, wykupując proponowane abonamenty i licząc na nagrodę w postaci opisanej w treści ogłoszenia. Jeśli dany pomysł nie osiągnie zakładanego pułapu w wyznaczonym czasie, wpłacane kwoty wracają na konta fundatorów.
Zortraxowi udało się uzyskać wsparcie 144 osób, a fundusze zdobyte dzięki nim to kwota 179 471 dolarów USA, a według wyliczeń potrzebnych było raptem 100 000 dolarów. Co więcej, cel osiągnięto przed zakończeniem zbiórki. Mogli rozpocząć budowę. Dzięki hojności fundatorów i zaangażowaniu pasjonatów powstała drukarka Zortrax M200.
Urządzenie to zyskało w dość krótkim czasie szaloną popularność nie tylko w Polsce, ale także na Świecie. Już w 2014 roku społeczność posiadaczy i użytkowników drukarek 3D, którzy zrzeszeni są na portalu 3DHubs.com, wybrali drukarkę 3D Zortrax M200 najlepszym urządzeniem Plug&Play, z jakim mieli do czynienia. Co więcej, urządzenie to uznano za jedno z 10 najlepszych tego typu urządzeń na Świecie przez magazyn „Make”!
Dzięki tym spektakularnym sukcesom i gorącym rekomendacjom zadowolonych użytkowników, w ciągu kilku zaledwie lat firmie udało się pozyskać klientów w ponad 50 krajach, co, jak na tak młody startup, jest nie lada wyczynem. Otwarto pierwszy tego typu salon firmowy w Warszawie, dzięki któremu można samemu przekonać się, jak działają urządzenia, dowiedzieć czegoś o technologii, zastosowaniach, a także kupić jeden z modeli wraz z akcesoriami, materiałami eksploatacyjnymi i częściami zamiennymi. Zortrax M200 kosztuje około 8000 zł, a M300 niewiele ponad 15 000 zł.
Wspomniany wcześniej salon firmowy to oczywiście jedno, ale w obecnych czasach nie można obejść się bez sklepu on-line. W nim także można kupić od drukarek, po materiały eksploatacyjne i części zamienne do urządzeń.
Swoje produkty firma Zortrax prezentuje także na różnego rodzaju polskich i zagranicznych targach, konferencjach, a także wszędzie tam, gdzie można pokazać zastosowania i jakość druku 3D. Ważne jest nie tylko tworzenie prototypów, ale także części zamiennych do różnego typu urządzeń, szczególnie takich, do których podzespoły nie są już produkowane, albo nie występują jako elementy do naprawy lub wymiany. Ciekawostką było zaprezentowanie elementów przydatnych w badaniach medycznych – model sztucznego serca, urządzenie do walki z żylakami.
Zortrax postanowił pójść jeszcze dalej i stworzył narzędzie, bibliotekę modeli i ich projektów, które można wykorzystać do przechowywania opracowanych projektów, a także dzielić się w nim spostrzeżeniami, doświadczeniami i liczyć na pomoc społeczności podczas tworzenia nowych planów obiektów.
Zortrax nie zasypia gruszek w popiele i kuje żelazo, póki gorące. A konkretniej pisząc, chodzi o nową drukarkę 3D – model Zortrax Inventure. Wprowadzono zamkniętą, podgrzewaną komorę roboczą, dzięki czemu znacznej poprawie uległa jakość wydrukowanych detali w modelach, co pozwala to na drukowanie szczegółowych modeli bez obaw o skurcz materiału". Dodano również drugą głowicę ekstrudera, pozwalającą na drukowanie rozpuszczalnego w wodzie materiału supportowego, dzięki czemu urządzenie może drukować ruchome i znacznie bardziej szczegółowe modele.
Dzięki wykorzystaniu w projektach podpór, które wykonuje się z materiału rozpuszczalnego w wodzie, poziom skomplikowania mechanizmów i kształtów wzniósł się na dużo wyższy poziom, niż było to możliwe bez tej technologii.
Same urządzenia nie byłyby niczym nadzwyczajnym, gdyby nie filamenty, czyli materiały plastyczne wykorzystywane przy tworzeniu modeli. Zortrax opracował je tak, by użytkownik mógł wytwarzać elementy twarde, plastyczne, matowe, błyszczące, kruche lub bardzo wytrzymałe, a na dodatek mające wiele kolorów.
Tworzenie nowych urządzeń, rozwiązań, a także materiałów eksploatacyjnych, to nie tylko samodzielna inicjatywa firmy Zortrax. To między innymi efekt współpracy z klientami i użytkownikami, którzy zgłaszają firmie różnego rodzaju pomysły, ale też zapotrzebowanie na nowe rodzaje filamentów pozwalającym im tworzyć to, czego oczekują. Firma chętnie wychodzi naprzeciw oczekiwaniom i motywuje swoich pracowników do pracy, a efektem są profesjonalne urządzenia, rozwiązania i materiały eksploatacyjne do każdej z produkowanych drukarek 3D.
Nic nie byłoby możliwe bez dedykowanego oprogramowania, które jest stworzone w sposób przystępny i przyjazny użytkownikom. Z-SUITE pozwala na ustawienie preferowanych parametrów wydruku i przekonwertowanie go na czytelny dla urządzenia plik *.zcode. (albo przekonwertowanie go na czytelny dla drukarki plik, umożliwiający stworzenie modelu). Z-Suite umożliwia między innymi na konwersję plików z projektami 3D do wersji pozwalającej na stworzenie modeli za pomocą drukarek Zortrax. Oprogramowanie współpracuje między innymi z programami takimi jak Autodesk 3DS Max,, Autodesk AutoCAD, Autodesk Maya, SketchUp, Solid Works, Cinema 4D, blender, Zbrush, Catia, Strata, LightWave i innymi. Można nawet pobrać wersję demo i spróbować swoich sił w obsłudze.
Wpis powstał we współpracy z Zortrax
30.06.2025 20:19, Rafał Chabasiński
30.06.2025 16:17, Rafał Chabasiński
30.06.2025 15:12, Katarzyna Zuba
30.06.2025 13:30, Mariusz Lewandowski
30.06.2025 12:55, Mateusz Krakowski
30.06.2025 11:32, Edyta Wara-Wąsowska
30.06.2025 10:57, Mariusz Lewandowski
30.06.2025 10:51, Rafał Chabasiński
30.06.2025 10:12, Katarzyna Zuba
30.06.2025 9:17, Edyta Wara-Wąsowska
30.06.2025 8:30, Rafał Chabasiński
30.06.2025 8:07, Edyta Wara-Wąsowska
30.06.2025 7:02, Aleksandra Smusz
30.06.2025 5:57, Rafał Chabasiński
29.06.2025 18:00, Rafał Chabasiński
29.06.2025 14:36, Miłosz Magrzyk
29.06.2025 12:35, Joanna Świba
29.06.2025 10:32, Miłosz Magrzyk
29.06.2025 9:31, Rafał Chabasiński
29.06.2025 8:17, Miłosz Magrzyk
29.06.2025 7:20, Rafał Chabasiński
29.06.2025 6:29, Miłosz Magrzyk
28.06.2025 19:08, Mateusz Krakowski